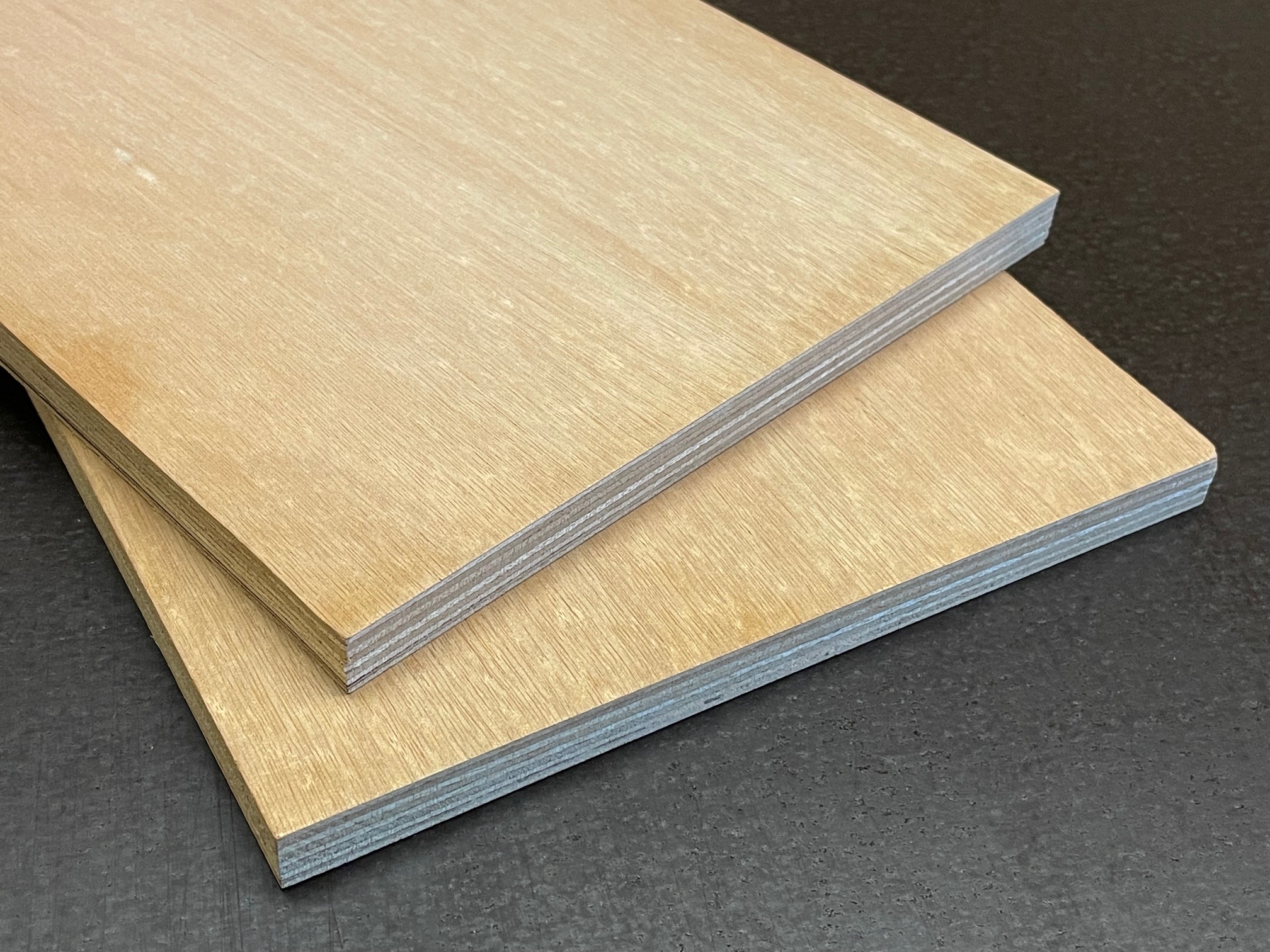
Our Marine Grade Okoume Plywood is manufactured to deliver exceptional performance in marine and moisture-exposed envionments, ensuring quality and durability of marine plywood.
Sizes Available
Offered in 8 ft x 4 ft sheets.
Custom made-to-order sizes available.
THICKNESSES:
Thickness | No. of Ply | Qty / Bundle* |
3 mm (1/8″) | 5 (3 + 2) | 300 |
4 mm (5/32″) | 5 (3 + 2) | 225 |
6 mm (1/4″) | 7 (5 + 2) | 150 |
9 mm (11/32″) | 7 (5 + 2) | 100 |
12 mm (1/2″) | 9 (7 + 2) | 75 |
18 mm (3/4″) | 13 (11 + 2) | 50 |
* Available in Less Than Bundle Quantities.
21 mm & 24 mm Thicknesses Available By Special Order
Why is the British Standard BS-1088 Important?
The British Standard is widely recognized in the boatbuilding and marine industries as the gold standard, as recognized by Lloyds of London.
This standard guides strict manufacturing standards resulting in consistent performance for demanding marine environments.
Okoume plywood USES:
- MARINE CONSTRUCTION
– hulls, decks, interior marine fittings - EXTERIOR ARCHITECTURAL PROJECTS
– decking, facades - EXTERIOR FURNITURE
- HIGH END CABINETRY
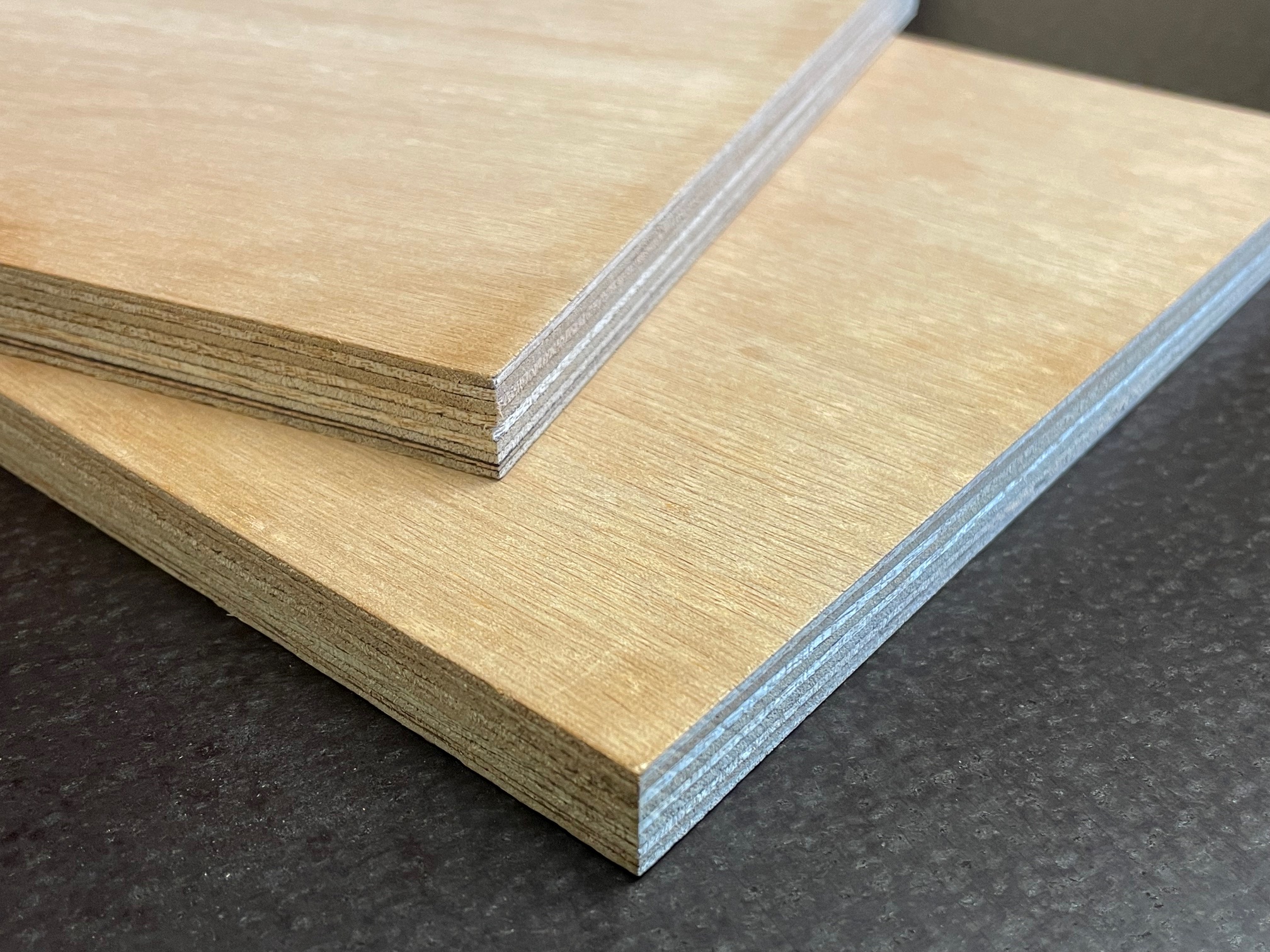
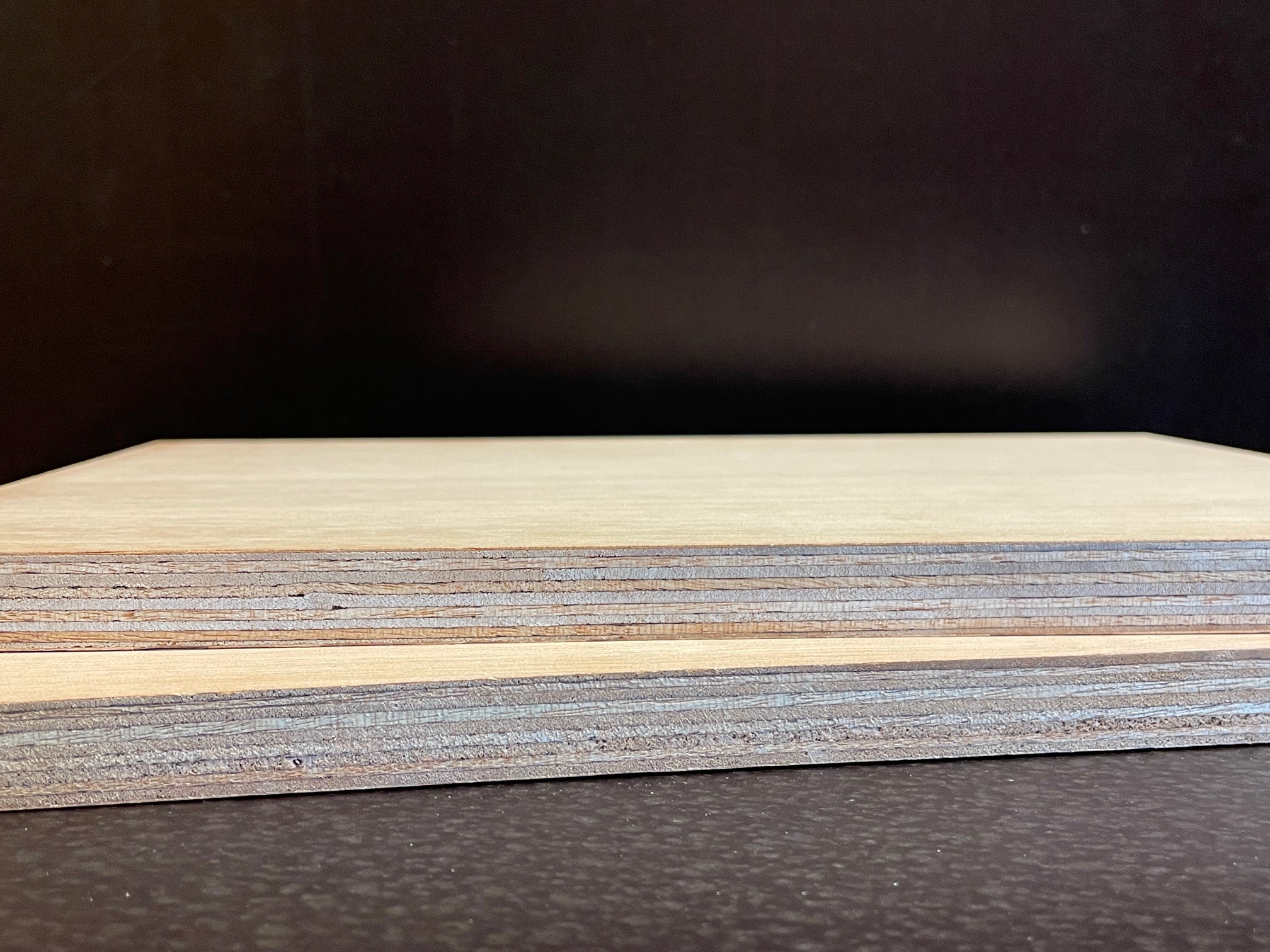
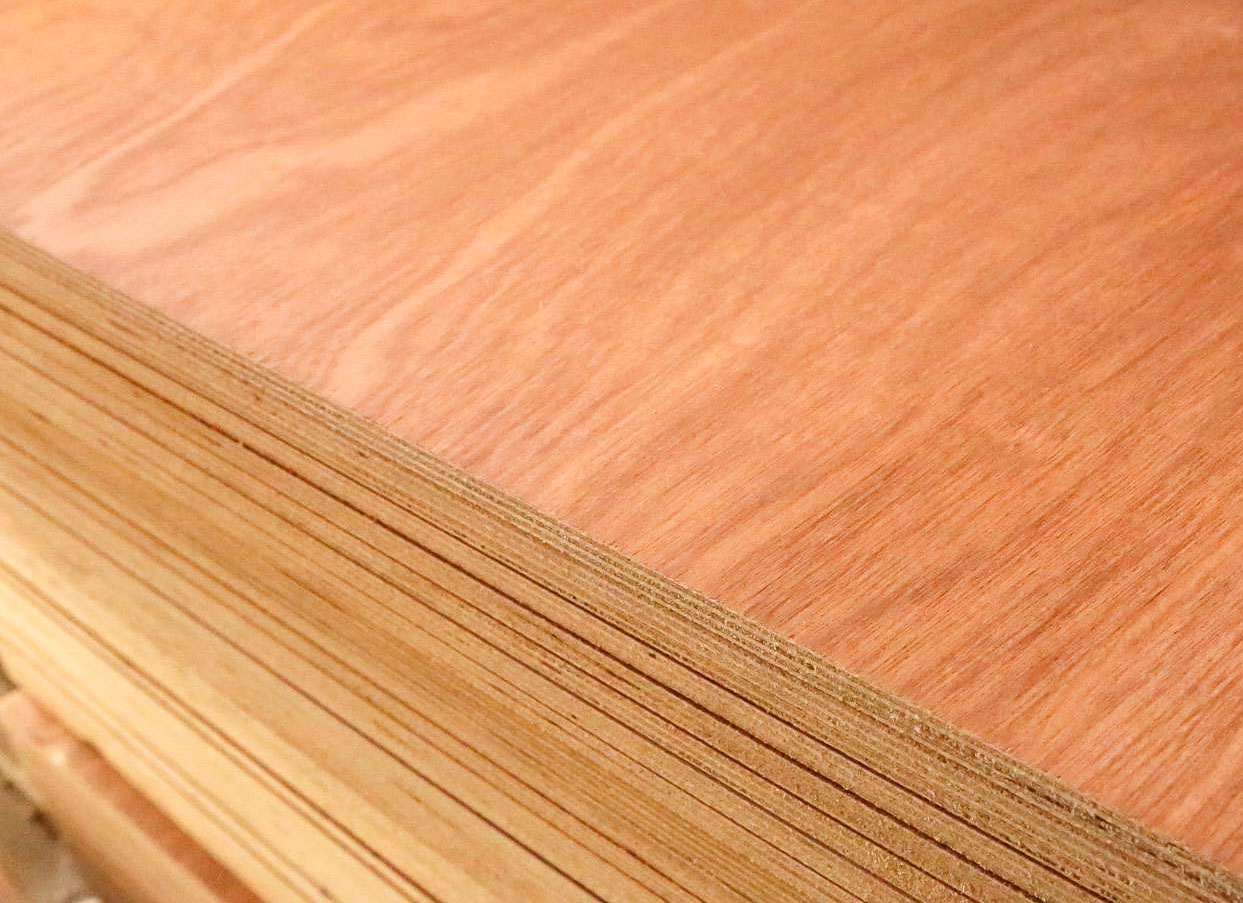
KEY FEATURES & REQUIREMENTS
Our Marine Grade Okoume Plywood delivers exceptional performance in marine and moisture-exposed envionments by adhering to these strict manufacturing standards:
1. Manufactured from durable High quality tropical hardwood veneers – No softwoods are permitted.
2. all veneers must be free from significant defects such as knots, voids, and splits – AND – must be uniform in thickness.
3. Each Ply Must Be Bonded Using a Weather AND Boil-Proof (WBP) Adhesive That Can Resist Immersion and Boiling Without Failure.
4. Plywood will have balanced construction, with each ply positioned at a 90-degree angle to adjacent plies to enhance strength and stability.
5. The faces must be free from open defects, including knots, cracks, and overlaps. Minor cosmetic imperfections are allowed on reverse side but not on the face.
6. Plywood must maintain structural integrity and resist warping or delamination when exposed to moisture and temperature changes.
7. Finally, sample panels are subjected to boil tests (usually 72 hours) to confirm adhesive integrity. Mechanical strength and resistance to fungal attack are also tested.
View Our
PRODUCT LIST
Our Commitment to
Sustainable
Sourcing
GET IDEAS